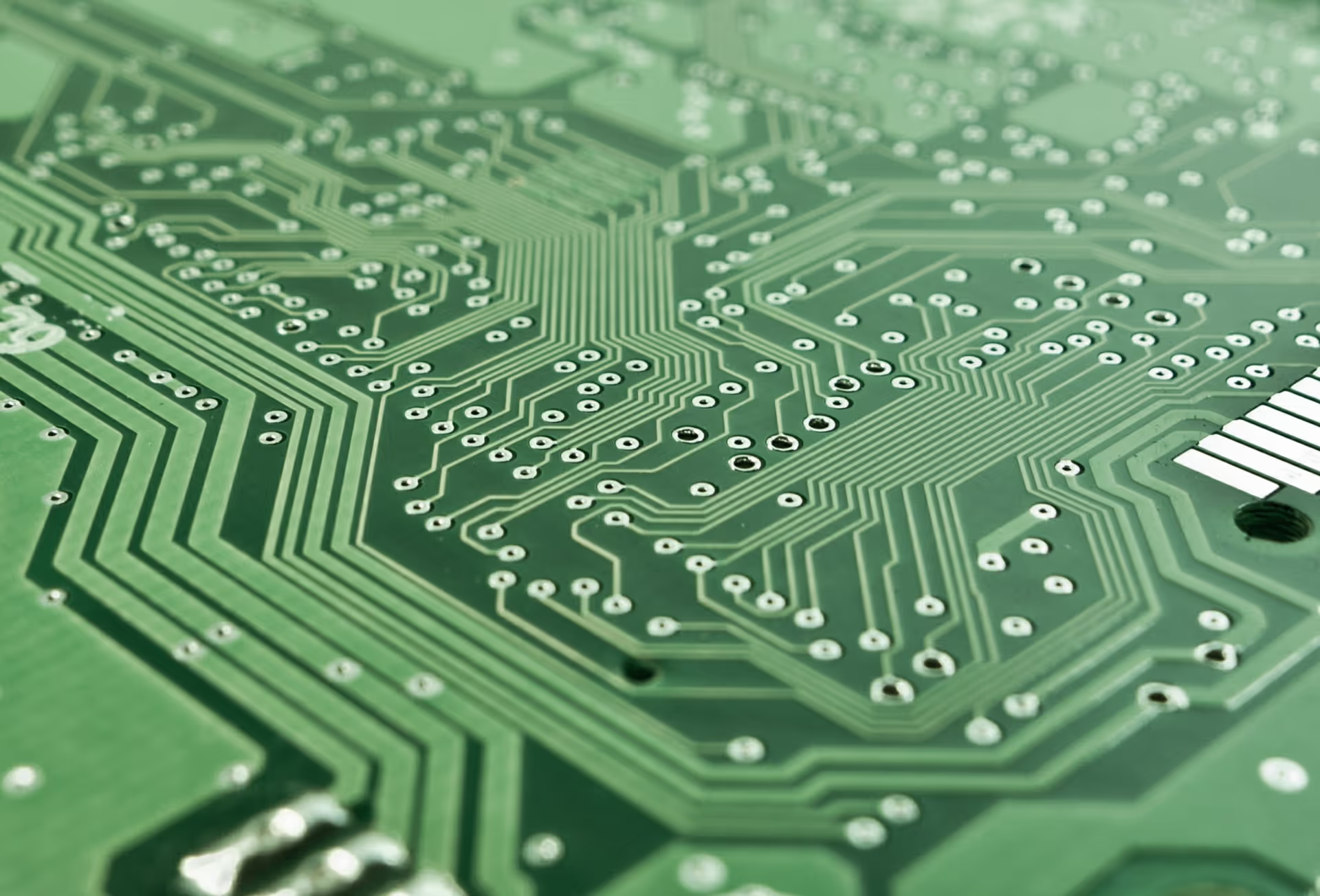
Have you tried using electrical prefabrication during the course of your work?
Like other areas of the construction industry, prefabrication is becoming more popular in the electrical industry. There has been a rise in the use of modular construction methods and prefabricated elements, with many pointing to improvements in productivity and a reduction in installation times for projects.
Prefabrication involves identifying repeated field installation tasks that can be constructed ahead of time. It’s a versatile construction method that allows greater flexibility than traditional construction methods.
In McGraw-Hill’s 2011 SmartMarket Report, “Prefabrication and Modularization: Increasing Productivity in the Construction Industry,” 35% of prefabrication users reported their project schedules were decreased by four weeks or more, 41% reported their project budgets were decreased by 6% or more, and 4% reported that construction site waste was decreased by 5% or more.
There are considerable reported savings and efficiencies to be made - is prefabrication worth it for electrical businesses?
Cost savings through prefabrication
One of the benefits touted by advocates of prefabrication is the cost savings. These can be made in a few different areas:
- Reduce material costs - Material cost savings through prefabrication can be made in a few different ways. For example, if you’re able to prefabricate common components for jobs, you can use any downtime in between jobs to do that work. This helps you to reduce overtime costs and expenses incurred on the jobsite.
Prefabrication can also bring cost savings through buying in bulk. If there are assemblies and components you can standardise across projects, you can often save money by taking advantage of special bulk pricing.
You can also argue that prefabrication helps to reduce waste, bringing cost savings and helping with green building goals (one of the motivations behind prefabrication). When you regularly build the same prefabricated components, you get very good at knowing exactly what you need. - Reduce labour costs - Prefabrication can help to reduce labour costs by preparing components ahead of field installation and reducing the chances of installation errors and rework. In some cases, you can even purchase prefabricated components from your suppliers, reducing the labour load on your company.
An Electrical Contractor Magazine article suggests that you can even save on labour costs by using less expensive labour to do the prefabrication work. (Assuming that they will be supervised by someone who is qualified).
There is also a suggestion that prefabrication can improve safety in the field, which can also be a labour cost savings. When you think of some complex electrical installations, you can see how installing something prefabricated may be quicker and safer. - Reduce estimating costs - Another possible cost savings can be made in your electrical estimating. When you use an estimating software, you can add prefabricated assemblies to your system and speed up your counting process even further.
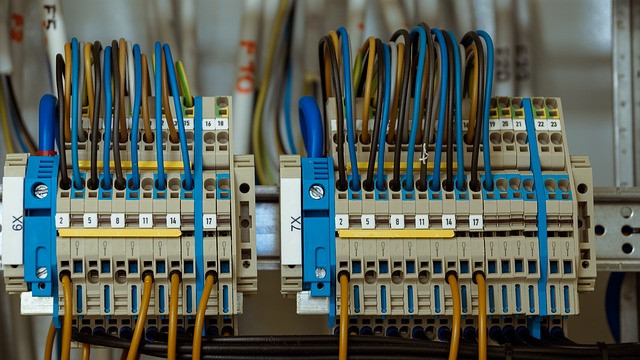
Time savings through prefabrication
One of the main benefits that advocates of prefabrication talk about is time savings on the job. When done well, use of prefabricated assemblies helps contractors to streamline their installation process, resulting in less time on the job site.
This means that prefabricated assemblies should be built to exact specifications so that there will be no need to adjust them on-premises. Some of the best examples only need to be connected to electricity to start working. This also saves time on ancillary issues, such as retrieval of forgotten materials or tools. Everything should already be there, ready to go.
Prefabrication can also eliminate unnecessary material handling on the job site. There is less moving of materials from room to room, like what happens with more traditional construction. As time goes by and your team is used to installing prefabricated assemblies repeatedly, they will tend to work more quickly and efficiently too.
If you have finalised plans early, you can potentially shorten the entire project timeline with prefabricated components. Some things can be prefabricated before a building is built or renovated, so the overall project timeline is reduced. Within different fields of construction, prefabricating can even help reduce the timeline by minimising weather impacts on construction. Something prefabricated in a workshop doesn’t need to be delayed by weather, like it might be if it were put together on the job site.
A recent example that has entered the UK and Ireland is the prefabricated data halls, produced by Schneider Electric. These customisable, modular constructions allow data centre owners to scale their operations without renovating or building new buildings. Instead, they can add on small increments to the prefabricated centres as needed. Installation is much quicker than starting from scratch.
Requirements for effective use of prefabrication
If you’re going to prefabricate components within your own company and it’s the first time you have done so, the overwhelming advice tends to be to start small. You might prefabricate wiring devices, temporary lighting or bending conduits, for example. The point is that by starting small, you can figure out what works and what doesn’t for your company, without there being some kind of disaster out in the field.
Advice from EC Mag states:
“The contractor must examine its current staffing, tools and facilities and then, if deciding to perform prefab work in house, must hire or train a person or staff to plan prefab activities, establish the appropriate prefab shop space, and ensure that the shop has the right tools and equipment.”
Secondly, it’s important to remember that prefabrication is an outcome of good project planning. It will succeed or fail based on the quality of the plan and the information that you have available going into the project. While prefabricated elements don’t need to be confined to only small items, you need to be very certain of what you’re doing when it comes to larger components. Any incorrect or incomplete specs or drawings could throw your project off-course.
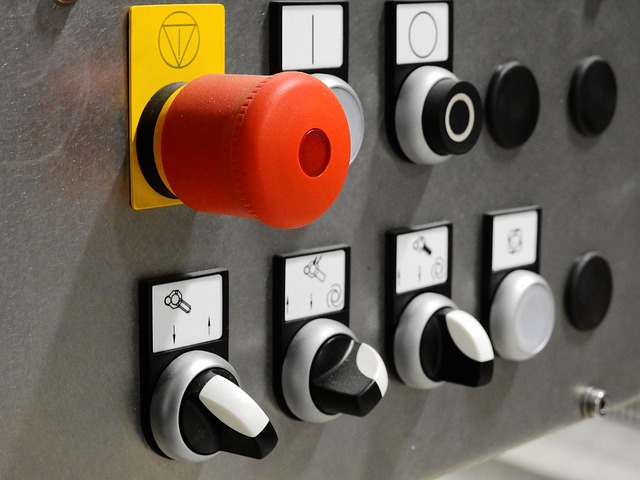
The future of electrical prefabrication
In the future of electrical prefabrication, it is expected that electrical will join and collaborate with other construction trades. For example, some companies are already integrating prefabricated electrical components such as panel builds and lighting packages into modular data centre skids, built by construction firms. Influences include factors such as green building initiatives and efforts to improve construction waste management.
One report indicates that global construction waste is predicted to double by 2025 - while it suggests that the UK and Europe currently lead the way for construction waste efficiencies, there is always room for improvement. We may see more incentive for companies to turn to prefabrication if rules around waste management tighten.
On the whole, use of prefabrication is relatively new to the electrical field, but it is catching on quickly. We expect to see it continue to grow as businesses seek better efficiencies.
Final thoughts
Is electrical prefabrication worth it for electrical contractors? On the whole, it seems to represent some decent savings in terms of costs and time, but of course the caveat is that you need a good plan to take advantage of it in the first place.
Where plans are incomplete or subject to change, prefabricating could create headaches - on the other hand, a strong, clear plan gives a good basis for prefabrication.
It’s also about having team members with the right training to understand prefabrication and be able to apply it effectively. Starting small can be a good strategy - learn what works for your company, then take it from there.